Reactions at Interfaces Initial wear Engineering down to the atomic scale
An important example, for instance, is the production of steel. In hot-dip galvanizing of steel – the technologically most important approach for coating steel with zinc – the formation of the so-called inhibition layer at the interface between the zinc coating and the steel surface plays an important role, and it is negatively affected by the presence of oxides on the steel’s surface.
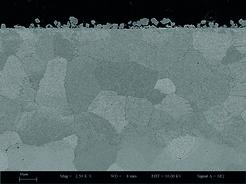
Fig. 1: SEM image of a Fe-2M%Mn-2%Si model alloy annealed at 700°C for 70 hours at partial pressure of oxygen just below the equilibrium partial pressure of Fe/FeO.
An example of the experimentally observed phenomena upon pickling (a metal surface treatment to remove impurities) which takes place after hot rolling, is a significant etching along grain boundaries. It can occur as a consequence of massive grain boundary oxidation during the cooling. Such a network of grain boundary oxide can be nicely seen as dark lines in Fig. 1. The extent of this grain boundary oxidation is sensitively affected by various alloying elements, with some combinations resulting in significantly enhanced grain boundary oxidation. These grain boundary oxides are usually found to consist of layers with varying stoichiometry.
Simultaneously, the physical reasons for the segregation of light elements such as oxygen to grain boundaries has been systematically investigated by ab initio calculations. We report here mainly about our research on nanocrystalline Ti, which is – among other applications – one of the most promising materials for human dental implants. Here, oxygen has also a pronounced, but positive impact on Ti properties. A segregation of a certain amount of oxygen is supposed to improve the thermal stability of grain boundaries leading to an increase of the yield strength by a factor of two.
For pure Ti, the symmetry of the atomic neighbourhood turns out to determine the probability that oxygen atoms will segregate to the grain boundary, while the amount of space that is locally available surprisingly plays a secondary role [1].
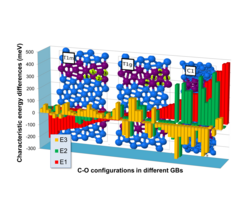
Fig. 2: Comparison of various C-O configurations in five different grain boundaries (GBs) in hcp Ti with (E1, red) O and C solved in the grain interior; (E2, green) O and C independently segregated to grain boundaries; and (E3) the pair formation in the grain interior (E3, yellow). Negative energy differences favour the formation of these configurations.
The observation that C is also a light element that is often found at these kind of defects raised speculations that a collaborative effect of O and C could substantially enhance segregation. We have therefore evaluated more than 70 configurations of O and C in the vicinity of five different grain boundaries (Fig. 2): 25 configurations are energetically more favourable than the solution of O and C in the grain interior (E1<0). The joining of independently segregated O and C atoms is for 33 configurations preferred (E2<0). And this pair formation yields for 42 configurations a larger energy gain than a pair formation in the grain interior (E3<0). In order to have a true co-segregation effect, however, all three energies need to be clearly negative at the same time. Since this turns out to be rarely the case, C does not promote grain boundary oxidation.
On the other hand we revealed by ab initio calculations that O strongly prefers Mn-rich environments in high-Mn steels. Therefore, we currently evaluate the hypothesis that the alloying with substitutional metallic atoms is more important for the segregation behaviour of O than the presence of other interstitial atoms.
Degradation mechanisms of mould material in experiments
Another example is precision glass moulding (PGM). PGM is a hot compression moulding process, during which the moulds experiences strong thermal and mechanical forces as well as chemical shock due to the direct contact with the aggressive molten glass. In such harsh conditions, the mould degrades rapidly and we are aiming to understand the fundamental mechanisms leading to its failure. To be more specific, we investigate the degradation mechanisms of a mould material made of cemented tungsten carbide protected by a PtIr coating deposited on an intermediate layer of Cr (PtIr/Cr/WC). This Cr layer serves at interlayer between the PtIr coating and the hard metal to ensure good adhesion of the former on the latter. However, during operation, the Cr layer degrades and Cr diffuses to the surface of the PtIr layer where its oxides cause the glass to stick to the surface, thus leading to quick degradation of the surface, rendering the tool unsuitable for the production of high quality lenses.
In order to investigate the degradation mechanisms and thereby find ways to limit or suppress them, a fundamental investigation of the underlying diffusion and oxidation mechanisms was initiated. To better control the oxidation conditions, we used an in-house designed furnace to expose the specimens to an extremely low pressure of oxygen (below 10-22 mbar). The nanometre-scale, three-dimensional, elemental and microstructural information were obtained using a combination of advanced microscopy techniques: atom probe tomography (APT) and scanning transmission electron microscopy (STEM).
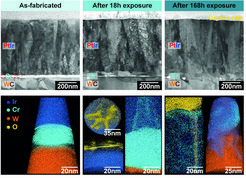
Fig. 3: Crosssectional STEM images and APT analysis of specimens after different periods of isothermal exposure at 630°C under an oxidizing atmosphere (PO2≈1.12×10-23 bar).
Fig. 3 shows a series of cross-sectional STEM images and corresponding APT analyses of samples after different exposure times. In the as-fabricated state, the PtIr coating, the Cr interlayer and the WC substrate can be clearly identified. Both interfaces, PtIr/Cr and Cr/WC, are sharp and flat, with no visible voids or cracks. After 18h of exposure at 630°C, although the Cr layer can still be distinguished, it has started mixing with the PtIr coating. Cr is seen to segregate to grain boundaries in the PtIr, and Cr-oxides islands are seen at the surface. After exposure for 168h at the same temperature, the original Cr layer has completely disappeared and was replaced by a series of voids. The local dissolution of the WC substrate has caused a roughening of the Cr/WC interface. A complete intermixing of the layers is also observed, with PtIr migrating downwards, while W penetrated into the PtIr layer. The interactions between PtIr, Cr and W within the interfacial region give rise to the nucleation of various intermetallic particles. The continuous supply of Cr to the surface through the grain boundaries allows for the growth of a 30–90 nm-thick surface oxide scale.
Based on our experimental observations, we schematised the evolution of the degradation process in Fig. 4. The nano-sized columnar grain structure of the PtIr coating provides numerous fast diffusion channels for Cr, accelerating the degradation progress. The newly formed Cr oxide scale on the one hand influences the morphology of the mould’s surface, and hence the surface quality of the final glass product; on the other hand, this oxide hampers the non-sticking property of the mould. Finally, the dissolution of the Cr layer and the formation of voids and intermetallic particles at the interface strongly impact the cohesion of the protective coating. Coating spallation frequently appears in practice, terminating the service lifetime of the mould. Ac-cording to the above-mentioned findings, measures to retarding the degradation process are being tested now, including using different types of interlayer and reducing the oxygen partial pressure in the chamber.
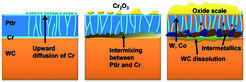
Fig. 4: Schematic illustration of the evolution of degradation.
This work has been performed in a collaboration with Fraunhofer IPT. This article shows a joint work of the MPIE departments “Computational Materials Design” (CM), “Interface Chemistry and Surface Engineering” (GO), and “Microstructure Physics and Alloy Design” (MA).
References:
CM authors: Dmitry A. Aksyonov, Poulumi Dey, Tilmann Hickel, Jörg Neugebauer
GO authors: Michael Rohwerder
MA authors: Z. Peng, Baptiste Gault