Ironclad climate protection
The metal industry and materials science have numerous possibilities to make metallic materials more climate-friendly.
Six percent of global CO2 emissions – 4.4. billion tonnes per year – are currently produced by the steel and aluminium industry. In an overview article for the journal Nature, Dierk Raabe, Director at the Max-Planck-Institut für Eisenforschung in Düsseldorf, and scientists from MIT in Cambridge Massachusetts outline how the immense CO2 footprint in metal production and use can be reduced. On the one hand, they propose measures that can be implemented quickly and with comparatively little effort. On the other hand, they formulate long-term goals that can be achieved only with the help of comprehensive basic research.
Modern societies would hardly be able to function without metals: alone 1.7 billion tonnes of steel and 94 million tonnes of aluminium are produced per year. They literally support industrial production, buildings, and transport as well as energy supply, telecommunications, and medicine. And by 2050, the amount of metallic materials produced and used annually could once again double – and even triple – for some materials. However, extracting metals from ores is extremely energy-intensive and produces huge amounts of CO2 emissions, thereby contributing to climate change. Steel and aluminium producers emit 30% of the greenhouse gases emitted by industrial companies worldwide. “We must reduce these industrial CO2 emissions”, says Dierk Raabe. “And the metals industry can make a significant contribution”. Not least because at least the industrial nations want to be largely climate neutral (i.e. have a positive CO2 balance) from 2050.
Growing demand for metallic materials and decreasing CO2 budget: In order to reconcile these scenarios, Dierk Raabe analyses how to reduce CO2 emissions in the metal industry together with MIT researchers C. Cem Tasan and Elsa A. Olivetti. “This is a task for both, industry and basic research”, says the Max Planck scientist. “For one thing, the metal industry already has opportunities to effectively reduce CO2 in the short term. However, there are still many potential areas for basic research in the development of sustainable alloys”. The scientists thus shed light on five fields in which industrial companies and researchers can – and must – become active:
More sustainability in production and processing
In order to reduce CO2 emissions in production, industry must recycle more scrap. Melting down a metal consumes considerably less energy than extracting it from its ore. “This applies above all to waste generated in the metal industry itself because large quantities are involved, and they can be separated relatively homogeneously”, says Dierk Raabe.
In the production of metals and their alloys, CO2-neutral processes are increasingly required. In this way, the respective ores can be electrolytically reduced directly to the corresponding metals with regenerated electricity. However, metals can also be obtained in whole or in part with the aid of regenerative hydrogen.
Companies can also save a lot of energy and thus CO2 when processing metals, especially by reducing the considerable losses that occur at all stages. For example, 40% of the molten aluminium is lost before it has even become a sheet of metal. In the case of steel, this scrap amounts to 25% at the very beginning of processing.
The city as a mine: sorting and recycling
In order to be able to increase the proportion of recycled metal, scrap must be better sorted since an alloy fulfils its function only if it does not contain too many impurities. Recycling therefore needs sophisticated techniques to identify, separate, clean, and crush alloys. Before these processes are perfected and competitive, research for the metal industry could develop alloys for which properties are hardly – or not at all – affected by impurities. Metallurgists are increasingly dedicating themselves to improving the possibilities of recycling.
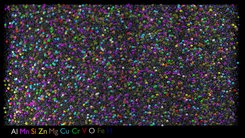
Sustainable alloy design for recyclable materials
On the one hand, researchers are already investigating alloys for various applications for which the properties are not significantly affected by impurities. However, they must first understand how the smallest traces of other elements can affect an alloy in which they should not actually occur. On the other hand, materials scientists are refining the possibilities of controlling the behaviour of metallic materials not only by their chemical composition but also by their micro- and nano-structure. When the number of alloys that differ chemically decreases, it becomes easier to separate and recycle scrap metal. In a similar direction, efforts are being made to compose crossover or unitary alloys. Such alloys should be able to perform various tasks for which specialized materials were previously developed. “Research into metallic materials is facing a paradigm shift”, says Dierk Raabe. “So far, alloys have been optimized for one-time use. Yet, in the future, we will have to put more consideration into recyclability when designing composition and properties”.
Longer life thanks to corrosion protection and repeated use
The ecological footprint of the metal industry can be drastically reduced simply by making alloys (or the components made from them) more durable. Fewer metals will have to be produced to replace them. “Above all, corrosion protection would have a huge effect here”, says Dierk Raabe. The metal industry and materials scientists deal with different types of corrosion depending on which metal is involved and in which chemical environment a material is used. This ranges from conventional rust or other forms of electrochemical corrosion to wear caused by heavy mechanical stress and hydrogen embrittlement. The efforts to counter them are as varied as the corrosive effects themselves. The industry protects many metals from electrochemical decomposition with sacrificial anodes (the material of which is corroded first). Materials scientists are also investigating alloys that heal cracks and other damage themselves by changing their micro-structure. They are also developing coatings that can eliminate (or at least mitigate) corrosion damage.
However, not all metallic components are discarded or replaced because they are worn or corroded. They must often give way for economic reasons. Using them elsewhere without first melting them down and then producing the same component again would also save a lot of energy. “In order to create appropriate recycling chains, appropriate incentives must be set at the political level”, says Dierk Raabe.
Energy efficiency through lightweight construction and better temperature resistance
The ecobalance of metallic products themselves can be improved by using them for as long as possible. However, energy can also be saved if the design of the materials and components is optimized accordingly. For example, cars with lighter bodies consume less fuel, and turbines that can operate at higher temperatures generate more efficient electricity from the heat of fossil fuels. In some cases, the efficiency of the application can still be improved by the design of the components; 3D printing creates new possibilities here. In many cases, however, metallurgists are once again called upon to develop appropriate alloys. By changing the composition and the micro-structure, they can increase the strength of the materials, reduce their density, or increase their resistance to high temperatures.
“Metallic materials are indispensable in a modern economy”, summarizes Dierk Raabe. “Fortunately, we have numerous opportunities to make them fit for a sustainable – and above all CO2-neutral – economy”.
Nature; 6. November 2019
Author: Peter Hergersberg, Max Planck Society