Intermetallic Phases & Materials
Intermetallic phases – intermetallics for short – are phases which have different crystallographic structures than the elements they are composed of. Compared to conventional alloys with a solid solution matrix, additional chemical bonding in the intermetallics usually results in higher melting points, significantly increased strength, and high wear resistance, however on the expense of ductility. Because of their low density and good oxidation behaviour, aluminides are of specific interest for the development of novel materials with enhanced properties. Fundamental research for the development of intermetal-lic materials is a long-term topic at the MPIE.
Limited ductility hampered a wider industrial use of intermetallic materials for long time. Breakthrough came with the application of γ-TiAl alloys for compressor blades in aero en-gines. Due to a fine-scaled lamellar γ-TiAl + α2-Ti3Al microstructure, they have a high specific strength. Basis for respective alloy developments is the understanding of the phase transformations leading to the formation of these microstructures and of the phase equilibria at high temperatures for the long-term stability of these microstructures during application. Investigation of phase transformations by differential thermal analysis (DTA) or high-temperature X-ray diffraction (HT-XRD) and evaluation of phase equilibria by electron probe microanalysis (EPMA) are therefore funda-mental for any aimed alloy develop-ment. Such essential thermodynamic data will be determined for a number of Ti–Al–X systems within the new large-scaled, collaborative European project ADVANCE. The MPIE not only has the facilities to determine the ther-modynamic data but also a variety of melting devices to produce the necessary high-purity alloys, e.g., by levita-tion melting. The results are used to generate an advanced ThermoCalc© data base, which is a design tool for the development of next generation γ-TiAl alloys.
Iron aluminides – an economic alter-native to stainless steels
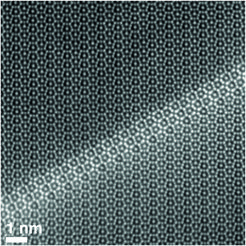
Fig. 1: High-angle annular dark-field scanning transmission electron microscopy (HAADF STEM) picture of a pyramidal fault in off-stoichiometric Nb-rich NbFe2 Laves phase.
Specific interest lies on the development of iron aluminide materials based on the phases FeAl, Fe3Al and the Heusler phase (X)2YA1 (X = Fe, Ni,...; Y = Ti, V, Nb, Ta,...). These materials have an outstanding corrosion resistance in a variety of aggressive environments, high wear resistance and low density and are considered as an economic alternative to stainless steels or Ni- and Co-based superalloys. However, limited strength at high temperatures inhibited any extensive application. New alloy concepts pursued at the MPIE lead to alloys which partially have much higher strength and creep resistance than advanced Cr steels.The alloy concepts include fine precipitation of borides or a film of Laves phase along grain boundaries, increasing the D03/B2 transition temperature, fine dispersion of Laves phase precipitates in the matrix, or generating coherent A2/B2/L21 microstructures. These developments have prompted new interest by industry. Casting, forging, and rolling on an industrial scale has been explored in a series of cooperations and different parts successfully passed tests under application conditions.
Additive manufacturing (AM) is a new technology by which near net-shape parts are generated by layer-wise melting of powders by a laser or electron beam. As intermetallic phases are highly wear-resistant and therefore difficult to machine, AM is an interesting alternative for producing parts from intermetallic materials. Within a large-scale collaboration with research institutes and German industries, AM of advanced iron aluminides was studied. Defect-free samples and parts were produced by different AM techniques and it was shown that basic alloy concepts developed for cast alloys can be transferred to AM. Also the possibility of generating chemically-graded samples by AM with a continuous variation of the composition between various stainless steels and iron aluminides could be demonstrated.
Laves phases - the most abundant class of intermetallics
Laves phases constitute the largest group of intermetallic phases. These very strong but brittle phases may not be usable as monolithic materi-als, but as strengthening phases, e.g. in iron aluminium alloys, Co-based alloys or steels. They exist with three different crystallographic structures, i.e. polymorphs, two hexagonal and a cubic. Stability of the different polymorphs in dependence on temperature and composition is another topic of basic research at the MPIE. An important aim is to un-derstand the variation of properties in dependence of the composition, as many Laves phases do have ex-tended homogeneity ranges and de-viations from the ideal composition leading to the occurrence of different types of structural defects (e.g., see Fig. 1).
It has also been shown that novel steels and iron aluminide based alloys are substantially strengthened by micron-thick films of Laves phase on the grain boundaries. Though the Laves phases are inherently brittle, no internal cracking of the films is observed after plastic deformation, e.g. creep. Transmission electron microscopy and local strain mea-surements by X-ray diffraction are currently employed to understand this phenomenon.
Corrosion resistance of iron aluminides
Iron aluminides show an outstanding corrosion behaviour and many investigations have been performed to unravel the underlying mecha-nisms. In all cases it has been found, that the ability to form Al2O3 scales or Al-rich passive films is the key for the excellent corrosion resistance. In oxidizing environments, thin, dense and adhesive Al2O3 scales form that also withstand thermal cycling. A minimum of about 15 at.% Al is necessary for their formation. Salt spray tests, corrosion in water vapour, aqueous corrosion, and hot corrosion by molten salts yielded varying corrosion resistance. However, in all cases an improvement was seen when the Al content was high enough to form protective scales or films. Al2O3 scales can also be generated by a short pre-oxidation treatment. The scales act as protecting “isolators”, separating the iron aluminide from the environment. Pre-oxidation has been shown to be very effective to enhance the aqueous corrosion resistance, which otherwise is only mediocre. The anodic current density in the passive range during immersion in H2SO4 of pH 1.6 is sig-nificantly decreased by two orders of magnitude and also repassivation of smaller defects occurs readily. X-ray photoemission spectroscopy (XPS) revealed that the scale is comprised of an outer layer of mixed Al and Fe oxides and an inner layer of hydrox-ides enriched in Al, which was found to be significantly more resistant than the oxide layers formed on pure aluminium. Even long-time immer-sing of the scale has no effect on its beneficial performance. Other intermetallics phases of interest for structural applications studied at the MPIE are silicides, NiAl and N3Al, of which the latter is the strengthening gamma prime (γ ́) phase in Ni-based superalloys.
SN Authors: M. Palm, F. Stein
GO Author: M. Rohwerder