Submicron Fracture Mechanics
Materials either fail by plastic deformation, by fracture or by a combination of both. The fracture process can be subdivided into three stages: crack nucleation, crack growth and, finally, the catastrophic failure. Today, the multi-scale nature of failure is well-understood: While the crack nucleation typically occurs at the microstructural length scale, i.e. at the level of single grains, phases or interfaces, the subsequent crack growth and catastrophic failure typically involves several different length scales. Former experimental limitations in analyzing cracks on the order of a few hundred nanometers prevented a thorough understanding of the small length-scale impact on device reliability. However, recent advances in producing micron or even submicron sized structures by focused ion beam (FIB) milling open new horizons in analyzing the first failure stage: the crack nucleation and crack growth at the microstructural length scale.
For this purpose, we, the Nano- and Micromechanics as well as the Nanotribology groups of the department Structure and Nano-/ Micromechanics of Materials (SN) produce micro cantilevers with typical dimensions of 1x1x5 µm³ and 200 nm deep artificial notches by FIB machining. The notch root radius is of the order of 10 nm. Subsequently, the samples are loaded inside a scanning electron microscope (SEM) by an in situ straining rig – with forces on the order of 1 mN [1]. For brittle materials, the load increases linearly until the local stress intensity at the artificial notch surpasses the material fracture toughness, i.e. critical strength against failure. The measured maximum force and the geometry factor (obtained from finite element simulations [2, 3]) are used to analyze the material dependent – but size independent – critical stress intensity factor, which is called fracture toughness. In case of semi-brittle materials, all plastic contributions to the energy dissipation have to be included. We are following the spirit of the internationally accepted ASTM standards for macroscopic testing (e.g. using a micro J criteria) by developing experimental methods at the micrometer length scale.
The micro cantilever can be placed in any location in a real microstructure: single grain or phase, individual interfaces. Functional material systems are of special interest to the SN department: semiconductors (like silicon [4, 5] or silicon nitride), biological composites, materials for high temperature applications [6] and hard coatings. Using these micro fracture experiments, we develop advanced solder materials that are promising replacements for lead based solders, which are banned due to health concerns [7, 8]. All these material systems predominantly fail in a brittle manner with a fracture toughness 1 - 4 MPa m1/2. In these materials, plastic deformation in the vicinity of the artificial notch, is neglected.
In contrast to the aforementioned functional materials, the structural materials of interest are known for their outstanding global fracture toughness. Still, some of the microstructural constituents – either formed while processing (e.g. martensite in dual phase (DP) steels) or introduced during service (e.g. white etching layers) – are known to be brittle. The focus of those studies is to provide reliable fracture properties of these small scale phases e.g. of a single cementite lamellae in pearlitic steel or of white etching layer in rails [9].
Our mechanical experiments are linked to advanced characterization by transmission and scanning electron microscopy, or by synchrotron based Laue microdiffraction. Hence, we evaluate the quantitative fracture toughness and determine the toughening mechanisms that are observed by characterization. Furthermore, environmental conditions (elevated temperature, hydrogen loading) are controlled in our experiments. These experiments create new horizons in understanding brittle to ductile transitions [5] or hydrogen embrittlement.
The knowledge of fundamental fracture properties of individual phases and interfaces at the microstructural length scale opens new prospects for the development of damage tolerant structural and functional materials, which is a central focus of the SN department.
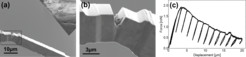
One example where the unique data obtained in our studies can directly be used is the project investigated by the collaborative research center TRR 188: "Damage Controlled Forming Processes". Within this research center we are working on DP steels and investigate the fracture toughness of 1 µm sized martensite islands as well as the fracture toughness of the ferrite-martensite interface. Combined with crystal plasticity modelling, we further identify locations at which damage initiation occurs. On the intermediate time frame we will use the local toughness values to control and optimize DP microstructures and the strain path during metal forming to avoid damage nucleation. Hence, based on our micromechanical investigations, we can provide devices produced via metal forming with known and optimized damage content. This will significantly reduce the weight and therefore increases sustainability of advanced steel parts produced via metal forming.
Another example which we perform in collaboration with the research group “Materials Science of Mechanical Contacts” is the characterization of the toughness of white etching layers (WELs, see p. 1-2). WELs and similar microstructures cannot be synthesized in bulk form, hence, without the micro fracture experiments developed in the SN department the fracture toughness would not be accessible. Based on these experiments fundamental insights into crack nucleation and propagation in instable microstructures such as the ones formed in the rail-wheel contact can be achieved.
References:
Authors: C. Kirchlechner, S. Brinckmann