Damage Mechanisms in Complex Tribological Environments
The contact between two solid bodies subjected to high forces under harsh environmental conditions and repetitive loading involves complex materials science phenomena (Fig. 1): Plastic deformation can lead to fatigue, grain refinement and precipitate decomposition. Frictional heat can cause diffusion, phase transformation, recovery or recrystallization. The presence of air, lubricants or body fluids at the contact point causes oxidation, the formation of tribolayers, or even corrosion or hydrogen embrittlement. These processes usually occur simultaneously while in service and cannot be tracked in situ. The analysis of such phenomena requires combined chemical and structural characterization down to the atomic scale.
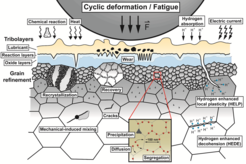
One main focus of the research conducted in Dr. Michael Herbig’s BMBF-funded group “Materials Science of Mechanical Contacts” is the investigation of white-etching-cracks (WECs), which are primarily known to cause failure in bearings and rails, but are in reality ubiquitous in high carbon steel applications subjected to intense mechanical contacts. Although this failure mode has been known for more than 100 years and causes enormous economic costs worldwide, so far neither is the mechanism understood nor are cost-efficient countermeasures available.
Our investigations showed that failure by WECs in rails and bearings involve fundamentally different conditions. In the case of rails, the comparison of experimental results with simulations revealed that each rail/wheel contact must be considered as an individual thermomechanical processing step of the rail. The high loads lead to high amounts of plastic deformation right below the contact patch in the rail. This is accompanied by frictional heating to peak temperatures exceeding 700°C that decay in a few milliseconds to ambient temperatures. The material changes accumulate during repeated loading of the rail, finally leading to a microstructurally altered, semi-brittle layer. Long fatigue cracks are generated when this layer fractures or partly delaminates [1].
In bearings the situation is fundamentally different. The significantly lower contact forces and friction causes the highest shear stresses to be found below the surface. Here cracks initiate at 60-90°C at flaws and eventually propagate to the surface to cause the part failure. Our research activities now have revealed that this failure is accompanied by a so far unknown crack propagation mechanism. Cracks have been known to continuously extend until failure occurs and this holds true also for WECs. However, WECs show additionally to that a unique particularity: they move through the material, viz. they continuously change their position, leaving behind a severely plastically deformed area. This so-called white etching area consists of nanocrystalline ferrite along with the segregation of carbon on the grain boundary. As WECs in bearings initiate within the bulk, the corresponding fracture surfaces are not oxidized. When WECs get in contact during a compressive loading cycle, strong adhesive forces form and material can be transferred from one side of the fracture surface to the other. Many repetitive loading cycles lead to a macroscopic change in the crack position [2].
The research activities on steels are complemented by investigations on hip implants where corrosion and wear debris at the contact zone between a titanium (Ti-6Al-4V) alloy stem and cobalt (Co-30Cr-4Mo) alloy head lead to adverse local tissue reactions. Here, the correlated use of the in-house high resolution techniques of transmission electron microscopy and atom probe tomography revealed that the passive film of the cobalt alloy can be torn off and be incorporated into the tribolayer of the titanium counterpart. The hence exposed fresh cobalt alloy surface corrodes, leading to the release of toxic Co into the human body [3].
Currently, cyclic mechanical contacts in liquid environments are often considered only in terms of stress fields, friction and lubrication flow. Our insights demonstrate the importance of material science aspects for the understanding of the related damage phenomena. Only when these additional factors are considered can the root causes of failure be determined and knowledge-based approaches to improve device reliability can be designed.
References:
[2] L. Morsdorf, D. Mayweg, A. Diederichs, Y. Li, D. Raabe, M. Herbig: Moving cracks form white etching areas during rolling contact fatigue in bearings, [under review in Acta Mater] (2019).
[3] S. Balachandran, Z. Zachariah, A. Fischer, D. Mayweg, M. Wimmer, D. Raabe, M. Herbig: Mechanisms of fretting wear leading to metal ion release in CoCr/Ti hip replacement implants: near atomic scale insights. [in preparation] (2019).
Authors: S. Balachandran Nair, M. Herbig