Nanocrystalline bulk steel with near theoretical strength: revealing the origin of its strength at the atomic scale
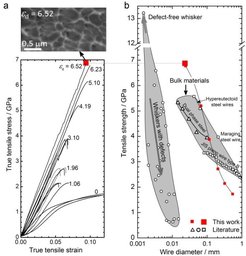
Fig. 1: Strength of cold-drawn pearlite. (a) True tensile stress-strain curves of cold-drawn wires for various drawing strains. The preceding true wire strain is indicated for each stress-strain curve. The inset shows a SEM image of a fracture surface after the tensile test of the most extremely cold-drawn wire, revealing dimples that indicate plastic deformation prior to fracture. (b) Comparison of tensile strength versus wire diameter for various high strength materials reveals that the most severely cold-drawn (εd = 6.52) pearlitic wire is the strongest bulk material known to date.
SPD is a scientifically and technologically important processing technique for producing ultrahigh-strength nanostructured materials, as shown in Fig.1 for the case of pearlitic steel wires where the tensile strength increases with increasing true drawing strain εd from 1 GPa at εd = 0 to nearly 7 GPa at εd = 6.52. The comparison of the maximum tensile strength of nearly 7 GPa with literature data for iron whiskers and other ultrahigh-strength materials reveals that cold-drawn pearlite exhibits the highest tensile strength among all known ductile bulk materials.
Cold drawing reduces the inter-lamellae spacing of pearlite, and consequently reduces the mean free path of lattice dislocations, which governs the Hall-Petch hardening and is mainly responsible for the strength of cold-drawn wires at true wire strains εd < 4. With further drawing, strong cementite decomposition occurs and phase boundaries partially disappear. Surprisingly, the strength of the mat-erial yet continuously increases with εd up to the experimental limit of 6.52. Clearly, the strength increase cannot be explained by the refinement of the inter-lamellar spacing any more. Here we explore the strengthening mechanism in this ultra-strong material and its microstructural origin via sub-nanometre scale characterization by atom probe tomography (APT).
Fig. 2 shows 3D carbon atom maps in longitudinal (left) and cross-sectional (right) views of samples drawn to low (εd = 2) and extremely high (εd = 6.52) true wire strains. It can be seen that the initially dominant two-phase lamellar pearlite structure observed at εd = 2 evolves, due to its dissolving cementite layers, into a carbon-de-corated ferrite (sub)grain structure, as is visualized by the carbon seg-regation at the ferrite boundaries (marked by blue arrows) at εd = 6.52. The (sub)grains exhibit a columnar morphology along the drawing direction and a nearly equiaxed shape with sizes below 10 nm in the transverse cross section. It is known that SPD-produced nanostructured materials are prone to dynamic re-covery and grain coarsening due to a large density of defects induced by SPD. However, for the present case these softening processes can be suppressed by carbon segregation at grain boundaries due to both the Gibbs adsorption effect and car-bon-drag preventing dislocation relax-ation. We found that the relationship between tensile strength and (sub)grain size obeys the same Hall-Petch law in the regime εd > 4.19 as in the low strain regime εd < 4. This indicates that the carbon-stabilized nanoscaled ferrite (sub)grain structure has replaced the role of lamellar structure in strengthening the present ultra-strong material at high drawing strains.
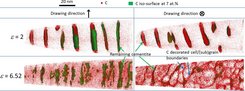
Fig. 2: Atom probe tomographic characterization of pearlitic steel wires cold drawn to two different true wire drawing strains of 2 and 6.52, respectively. 3D carbon atom maps in both, longitudinal (parallel to the drawing direction) and transverse cross section views (perpendicular to the drawing direction). Green and blue arrows mark the remaining (partially chemically decomposing) cementite and some of the (sub)grain boundaries decorated with carbon atoms, respectively.
To stimulate new ideas for the design of ultrahigh strength materials we emphasize the essential role of the second phase, e.g. cementite in pearlite. Via wire-drawing induced mechanical alloying the second phase chemically decomposes and acts as a supplier of solute atoms, which segregates to the (sub)grain boundaries stabilizing the nanoscaled grain structure, thus enabling an enormous strength of the drawn materials.
The key mechanical consequences of severely deformed pearlitic steel wires are including microstructure refinement and cementite decom-position but there are other effects that should be taken into account when high levels of strain are applied. APT measurements have shown that the concentration of carbon is not only increasing in the grain boundaries but also in the ferrite grain interiors and it exceeds the equilibrium solubility limit by far. As a consequence, more and more carbon stemming from the decomposing cementite must be partially accommodated inside the ferrite grains during the wire-drawing process. Thus a fundamental question arises: where do carbon atoms prefer to be located?
One of the experimental goals of the SN Department in this study is to link the observed cementite decomposition with structural evolution of the ferrite phase upon the drawing process. X-ray diffraction techniques provide one of the non-destructive methods for determining structural parameters of materials such as crystal structure, crystallographic texture and residual stresses. In this project, synchrotron radiation is used to probe the wires with much higher accuracy than laboratory X-ray diffraction. Upon wire drawing, high residual internal stresses are produced in the wires and a strong crystallographic texture develops which cause a drastic change in the mechanical behaviour of the steel wires. Furthermore, the study of the mechanical contribution of each phase in the wires is needed in order to characterize the load distribution between the ferrite and the cementite phases. For that purpose, in situ tensile tests coupled with synchrotron XRD are performed allowing for directly measuring the lattice strain evolution of the individual phases during deformation. Quantifying the load sharing behaviour of severely drawn pearlitic steel wires makes clearer the contribution of each phase on the global mechanical behaviour and stimulates new ideas for materials strength optimization.
Authors: Soundes Djaziri & Yujiao Li