New high performance steel with potential applications in the automotive industry
The requirements for steels applied in the automotive industry are manifold: strong steels are used for centre pillars, the part of a car installed next to the driver’s door. On the other hand, the front part of a car must consist of strong and at the same time ductile material. Thus, in case of a crash, the shock energy can be absorbed and the driver is protected. Dr. Dirk Ponge, group leader at the MPIE, has achieved to combine both requirements in one class of new steel, named “lean maraging TRIP steels”.
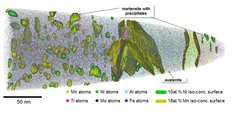
Result of an analysis by the 3D-atom probe. The martensitic and austenitic phases are visible. Even single atoms are recognized by this technique – each dot represents the location of one atom while the surfaces are regions of iso-concentration of a certain element.
Due to a high nickel content conventional maraging steels are very strong and used in air plane landing gear. The term maraging merges ‘martensite’ and ‘aging’. The name is derived from a special heat treatment (aging) which strengthens an already quite strong martensite structure. ”The use of a high amount of nickel results in a strong steel, but also caused an expensive production.” That’s why Ponge reduced the nickel content and found a surprising effect.
Combination of strength and ductility
During heat treatment, the formation of intermetallic precipitations causes an increase in strength. At the same time austenite is formed which is the reason for the increase in ductility and the basis for a second effect: the TRIP effect. TRIP stands for transformation induced plasticity. Triggered by a deformation process, a phase transformation from metastable austenite to martensite takes place in the material. This leads to an increase in strain hardening rate and enables to reach high elongations. With both these effects occurring, one obtains a good combination of tensile strength and total elongation up to 30.000 MPa%. The intermetallic precipitations, which are responsible for the excellent properties are analysed with the 3-dimensional atom probe.
Optimisation by computational materials design
Currently, the development of these steels is being optimised. Ponge expects to further decrease the production costs and to improve the mechanical properties by modifying the alloy composition. This is performed in close cooperation with the department of Computational Materials Design. The department of Prof. Jörg Neugebauer is calculating with the means of quantum physics, which precipitations are formed in the material with respect to the composition. This improves the efficiency of the further development and reduces the number of experiments. A systematic and application-oriented development of the lean high-performance steels is on the way.
Author: Dirk Ponge