Nano-beads for the steel forge
The crystal structure of metals can change at linear defects, which should affect the properties of the materials
Steel has already been around for roughly 3000 years and in several thousand variations today - yet it is always good for a surprise. Scientists at the Max-Planck-Institut für Eisenforschung in Düsseldorf have now made a discovery in manganese steel which is thought to affect the properties of the material for good and bad. They have found out that the alloy forms a different crystal structure at linear defects than is typical for the material. The individual crystal grains of which any metal is composed can be considered as a stack of individual atomic layers. Linear defects, or more precisely edge dislocations, occur when a layer remains incomplete so that the layers above and below it must take a step. As the length of the linear defects in a cubic metre of steel can add up to one light year, the discovery ought to have great practical significance since the structure of a steel depends on, among other factors, how malleable, rigid and ductile it is – properties which material scientists want to continuously optimize.
Dislocations can save lives. This stems from the fact that the one-dimensional defects in a metal play an important role when the material deforms: for example, when a car body panel crumples in an accident, thus absorbing a large part of the impact energy and hopefully protecting the passengers from injury. In such a case, the dislocations act as nano-hinges along which a metal bends. The fact that the crystal structure differs from the structure immediately around the linear defect should therefore also affect how the metal deforms. In the worst case, it tears rather than deforms. “We don’t yet know what effect the spatially confined chemical and structural states in the material have on its properties,” says Dierk Raabe, Director at the Max-Planck-Institut für Eisenforschung and head of the study in which the deviationists in the microstructure have just come to light.
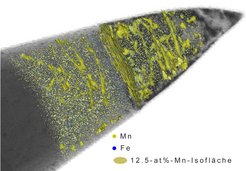
“We stumbled across the states more by chance,” says Dierk Raabe. He and his team had been investigating the micro- and nano-structure of a particularly rigid and ductile manganese steel which is strengthened with the aid of nanoparticles and is used in the landing gear of large aircraft, for example. They analysed this material with the aid of atom probe tomography. The analysis involves a sample being vaporized atom by atom with short pulses of an electric voltage. From the time-of-flight to a detector it is possible to determine to which element the vaporized detached atom belongs; its position in the sample can be determined from the location where the atom impinges on the detector.
The researchers found chains of manganese-rich nano-beads in the steel
“We noticed that the concentration of the manganese increased along specific lines after we had heated the material,” explains Dirk Ponge, who made important contributions to the study. The fine tubes in which the manganese collects are only two nanometres wide. And this happens not along the whole length, but more in the form of a chain of manganese-rich nano-beads.
In order to accommodate the larger number of manganese atoms in these minute areas, the crystal structure of the material must change. Iron and manganese atoms normally sit at the corners and centers of a cubic unit cell, the smallest structural unit. The researchers call this a body-centred cubic or martensite structure. The manganese concentration in the chain of nano-beads corresponds to an arrangement in which the atoms are located on each face and corner of the unit cell, in technical terms, a face-centred cubic or austenite structure.
Previously, material scientists only knew such deviations from the regular crystal structure of a metal in two-dimensional form, i.e. from the boundaries of the individual crystal grains which form a material. But why did they find filigree austenite structures in the interior of individual martensite crystal grains? “When we saw that the manganese accumulated in thin tubes, we had the idea there could be spatially confined chemical and structural states along linear defects,” says Dirk Ponge.
The different crystal structure at the defect helps to save energy
In order to be certain, he and his colleagues first scanned an iron-manganese sample in a transmission electron microscope, which makes linear defects clearly visible. They then mapped the distribution of the atoms in the sample again with the aid of atom probe tomography. And on the superimposed images from both methods they actually did find how the manganese-rich nano-beads arrange themselves precisely along the linear defects.
The fact that the atoms arrange themselves differently from the remaining crystal precisely along the dislocations is also suggested by an explanation of the observation: “The stress is particularly high at the dislocations,” says Dirk Ponge. “The material can apparently reduce stress and thus assume an energetically more favourable state by forming a crystal structure there which would be energetically less favourable otherwise.” On the basis of this finding, the Düsseldorf-based researchers extended a key formula that material scientists use to calculate which structure a material favours under which conditions at such structural defects.
Can a Damascus steel forge itself?
The researchers had first to mobilize the atoms with heat so that the atoms could assume the structure which is energetically more favourable there, directly at the dislocation, and only there. “This doesn’t mean that the spatially confined chemical and structural states form only when heat is applied, however,” says Dierk Raabe. These states can therefore probably not only be found in the cylinders of a motor, the blades of a turbine or other materials that are permanently subjected to great heat. “Small atoms, such as those of carbon, are much more mobile than those of manganese,” explains Dierk Raabe. “We therefore must assume that we will find the spatially confined states in carbon containing car body steel panels as well.”
The researchers now want to investigate what effect the local structural change has on the properties of a material. “Our findings may help to explain an already known behaviour of metals – the fact, for instance, that metals become brittle when they corrode and absorb hydrogen,” says Dierk Raabe.
However, it’s not always bad news when the crystal structure at linear defects steps out of line. “Maybe we can bring about these spatially confined states intentionally in order to develop a nano-Damascus steel that forges itself,” says the Max Planck Director. Damascus steel received its name because it came to Europe via Damascus. Expert craftsmen in the Orient forged a hard, yet brittle, and a ductile, yet soft steel into a composite material which is hard, but does not break easily. In future, a simple way may be found to combine these actually incompatible properties, if dislocations could be used to help provide a structure. This would open up completely new possibilities for the steel industry to optimize a material for a special application in an even more targeted way.
Author: Peter Hergersberg (Max Planck Society)