Disorder creates rust protection
A material's nanostructure is decisive in determining how resistant it is against corrosion
Corrosion eats away 75 billion euros of economic output annually in Germany alone. But it may soon be possible to better assess which steels and other alloys will be affected, and how to limit the damage: An international team led by scientists from the Max-Planck-Institut für Eisenforschung GmbH in Düsseldorf analysed an amorphous steel comprising iron, chromium, molybdenum, boron and carbon. They found that the more ordered a material’s structure is, and the more uneven the distribution of its atoms, the more easily it is corroded by rust. If the elements of the alloy don’t form a regular crystal lattice and are distributed completely uniformly across the material, then, under corrosive conditions, a passivation layer forms on its surface and protects it from rusting. If, in contrast, ordered nanocrystals form that sometimes contain more chromium and sometimes more molybdenum, the corrosion quickly eats away the material because no protective passivation layer forms. These findings give materials scientists clues as to what they should pay attention to regarding the composition and production of materials.
In humid air, chemistry gnaws at every metal, unless it happens to be gold or another precious metal. But oxygen in the air is only too happy to hook up with the less precious representatives of this class of materials. Humidity helps it in its search for a partner, and all the more so the saltier it is. At the outset of a corrosive attack, some metals, such as chromium and zinc, become coated with a dense oxide layer that prevents further advances on the part of the oxygen. If no such passivation layer forms, the metal corrodes, leaving behind a porous and brittle surface that causes a car body or a ship’s hull to gradually crumble. This is how corrosion destroys up to 4 percent of the economic output of the industrialised nations every year.
“Our findings explain why some materials are particularly susceptible to corrosion despite having the exact same composition as corrosion-resistant steels,” says Frank Renner, who headed the study at the Max-Planck-Institut für Eisenforschung GmbH and is now a professor at Hasselt University in Belgium. It is still difficult to say anything about the corrosion resistance of alloys that are currently used in automotive manufacturing, shipbuilding and plant construction. These materials have numerous components. How resistant they are to corrosion depends not only on their composition, but also on how the material was processed and what temperature it is exposed to in use, for instance in a power plant turbine.
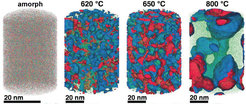
A model for the transition from amorphous to crystalline steel
The team of Max Planck researchers has now comprehensively investigated for the first time how the micro- or nanostructure of an alloy that chemists describe using the formula Fe50Cr15Mo14C15B6 influences its corrosion resistance. This alloy is one of the amorphous steels that are used, for example, as abrasion-resistant coatings. The elements in it are present in an irregular structure, but they are distributed completely uniformly in the material. “We are interested in the alloy primarily as a model system in which we can study the transition from the amorphous form to the crystalline form,” says Frank Renner. Since it’s similar to common chromium-molybdenum steels, the researchers’ findings are also relevant for materials used in actual practice. The researchers’ test alloy does, however, contain significantly more carbon than common steels, and also the high boron content is rather unusual for steels from the blast furnace. However, this was the mixture that allowed the team to produce the amorphous variant of the alloy.