Micromechanics of large deformations
- Date: Jun 10, 2021
- Time: 01:00 PM - 02:00 PM (Local Time Germany)
- Speaker: Dr. Ing. Napat Vajragupta
- Group Leader Interdisciplinary Centre for Advanced Materials Simulation, Ruhr-Universität Bochum, Germany
- Location: Online
- Room: Virtual Lecture
- Host: Dr. Maria Jazmin Duarte-Correa
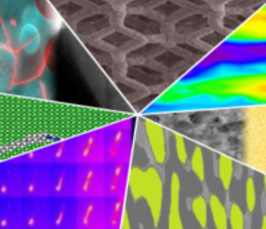
Understanding of the influence of microstructural features on mechanical
properties of materials is essential for designing new materials and
optimizing manufacturing process like sheet metal forming process. To
gain the required knowledge, a large series of experiments are typically
employed, which is economically rather inefficient. In this context,
micromechanical modeling supports the development of required knowledge,
by predicting the mechanical behavior of materials through
microstructure-based simulations. This work aims to demonstrate the
possibility of using micromechanical modeling to understand the
influence of microstructural features on the mechanical behavior of
materials at different scales. First, we introduce a software package to
generate synthetic microstructure models which can mimic grain geometry
and texture. For the latter, we develop a method to reconstruct the
orientation distribution function (ODF) and the misorientation
distribution function (MDF). With respect to the material model, a
non-local crystal plasticity model is incorporated to describe the
plastic deformation of the polycrystal. However, a number of material
parameters are large which result in great difficulty in defining a
unique set of material parameters. We hence develop a robust
optimization scheme to parameterize a non-local crystal plasticity model
from nanoindentation test. A synthetic microstructure is then treated
as a model for finite element analysis with a parameterized non-local
crystal plasticity. With this way, we are capable of predicting
mechanical properties of the material such as anisotropic plasticity and
strain hardening behavior under complex load paths. We can also
investigate the influence of key microstructural features such as grain
geometry and textures, and defects like pores on corresponding
mechanical properties. Furthermore, local deformation fields of the
location of interest are captured from the macroscopic simulation of the
bending process and imposed as boundary conditions on a synthetic
microstructure to study the changes in the microstructure during the
manufacturing process. Finally, microstructurebased simulations are used
to create training data for machine learning models that are able to
predict microstructural properties to a given flow curve