
Research
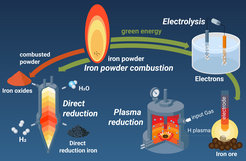
Metallurgy has provided humankind since more than five millennia with materials, tools and the associated progress. It is not only a huge engineering success story, but has also become the biggest single industrial environmental burden of our generation. Disruptive innovations are required for alternative reduction processes that convert mineral ores into metals without today’s carbon based methods that release huge amounts of CO2. The International Max Planck Research School for Sustainable Metallurgy (IMPRS SusMet) focuses on the exploration of carbon-free sustainable metallurgy, employing hydrogen, ammonia and other H-carriers as the reducing agents, direct reduction, plasma synthesis and electrolysis.
The IMPRS SusMet covers the the following focus topics:
- Chemical processes: redox reactions under confined dimensions and high mechanical stresses, hydrogen storage in the reduced materials, phase transformations and induced cracking, aluminium/iron electrolysis, transport, nucleation and growth processes
- Mechanistic processes: formation of amorphous metal foams and sponges under high-temperature reactive conditions and origin of nano-/meso-/macropores, cracking due to high steam pressures, oxygen percolation and transport
- Plasma processes: hydrogen and ammonia plasma reduction, interplay of plasma reduction and slag formation
- Scaling: characterization of metallic sponges from direct reduction processes, transfer of the nanoscale reaction analysis to large-scale reactor design
- Secondary synthesis: novel alloys that are tolerant against compositional changes so that they are more amenable to recycling, foundations of electrolytic recycling of complex multi-component scraps
- Longevity: mechanical, thermodynamic and chemical degradation, high temperature, aqueous and non-aqueous corrosion, stress-corrosion cracking
In order to understand reduction processes in metallurgy and identify sustainable primary and secondary synthesis approaches, the doctoral students are part of an expert team at one of four research institutes which develop new advanced experimental, analytical, in-situ, multi-probe, in-silico and synthesis techniques:
- High resolution analysis, monitoring and modelling of chemistry, structure and transformations at the atomic scale of buried interfaces and defects by correlated experimental and simulation techniques in both space and time (e.g. correlated transmission electron microscopy, atom probe tomography and machine learning augmented analysis techniques)
- Simulation of materials structures and properties over all relevant length scales, from the atomic scale over the meso- to the macroscale (e.g. cutting-edge ab initio methods, scale-bridging / multiscale approaches, machine learning and big data, high-throughput techniques, simulation-guided synthesis and microscopy, materials design and discovery)
- Interplay of transport and reactivity across all relevant length scales
- Local and global mechanical properties
- Electrochemical, kinetic and thermodynamic properties
- Electrical and magnetic properties
- Synthesis of all required sample materials, reaching from high-purity single crystals to complex alloys and oxides
- Laboratory-scale reactor design for both primary synthesis from mineral ores and secondary synthesis from scraps
As a basic research initiative, the IMPRS-SusMet focuses on understanding the fundamental aspects of sustainable synthesis processes. The transfer of already existing knowledge into industrial applications is explicitly outside the scope of IMPRS SusMet. The new knowledge to be created within IMPRS-SusMet, however, will have wide-ranging applications in novel processes and materials for the upcoming hydrogen infrastructure of the 21st century, light-weight and high-temperature materials.
Curious? Get to know us at one of our annual interview sessions.